Demolition + Framing
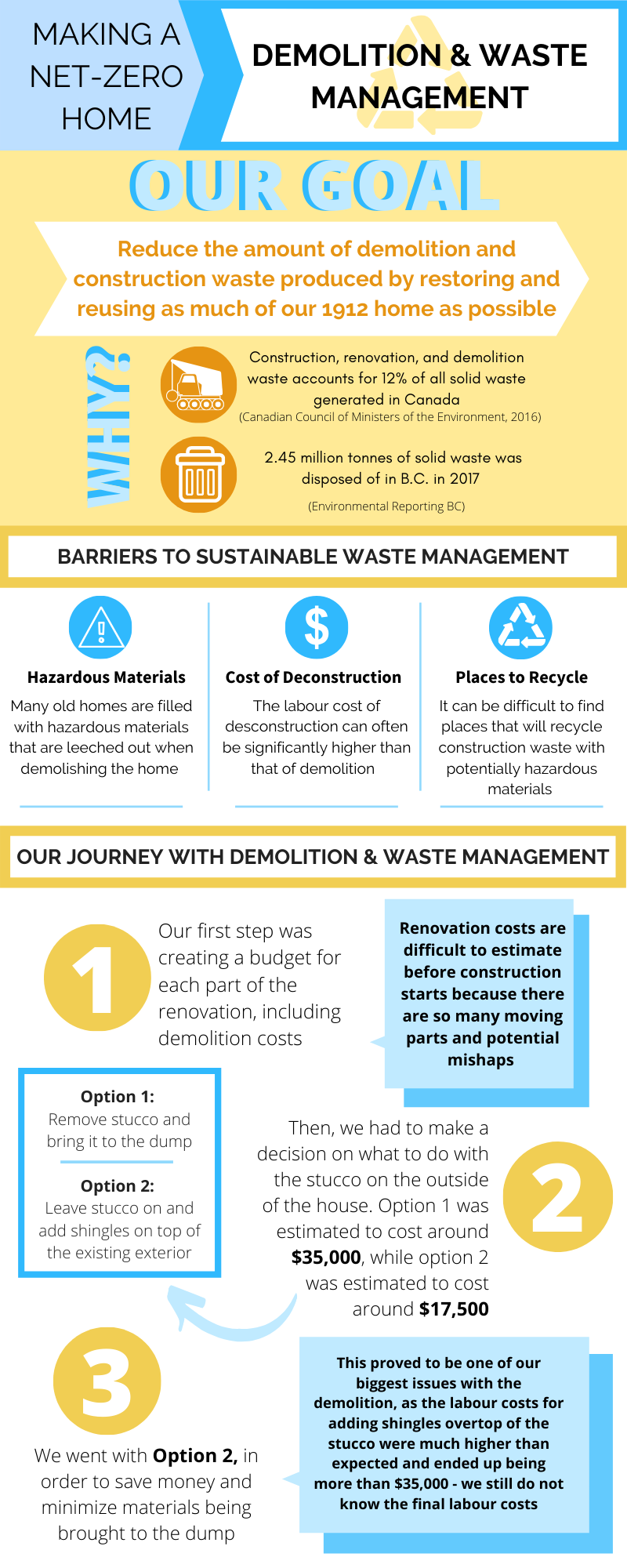
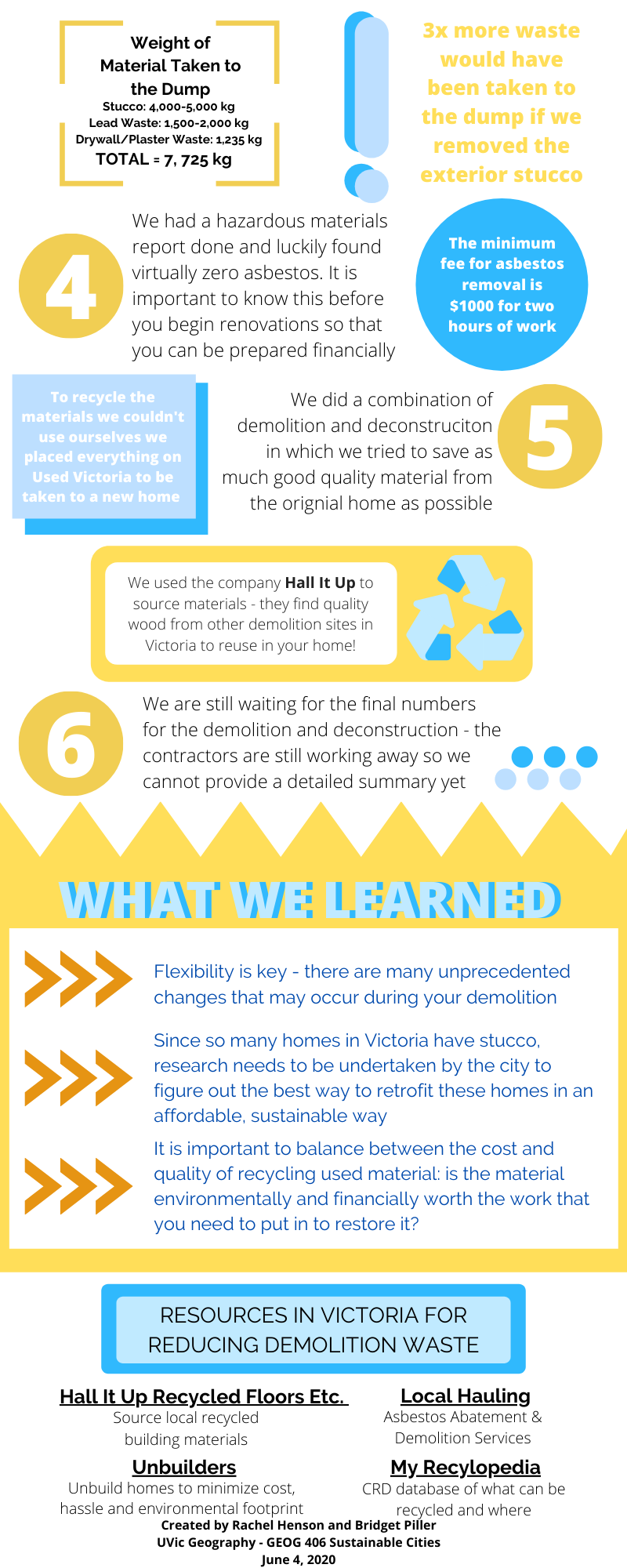
There was a carpet (1990) over linoleum (1940) over subfloor over original fir (1912). Sad to see this linoleum go the way of the dropped ceiling and paneling and fiberglass insulation.We are laying a new fir floor downstairs but patching and painting the floor upstairs.
Demolition and Keeping Stucco out of the Dump
The lovely infographic above was researched and designed in June 2020 by Bridget Piller and Rachel Henson, students at University of Victoria in Cam Owens Geography class on sustainable cities. Working with students and the university (three separate times during the course of the build) has been a rewarding and fun aspect of our project. We are trying to make the house an example for others to learn from. The talent and enthusiasm the students bring to the task makes that assignment much easier.
We knew we were staring at a major undertaking. The House’s 1912 building materials - first growth fir (likely 300 years old) were great. We saved as much wood as we could to repurpose in the renovation. An outside firm (Local Hauling) did the major demolition in a matter of days - starting at the end of September 2019. Still there was quite a lot of prep work for contractor Taylor MCarthy’s Frontera crew to do before framing could begin. Local Hauling’s owner, Shawn Dodge can be reached at 250-589-4054.
Architect, David Scott, came from Vancouver in October once the demo was essentially complete to look forward to framing. Olivia Bull, designer at Scott & Scott began to get more and more involved in the project working in tandem with our contractor, Taylor McCarthy to cross reference what is on the plans with the realities of conditions on the site. We had weekly meetings on the phone or via zoom to keep everyone in the loop, troubleshoot and set priorities. Sometimes for these meetings, Don and I were in Victoria, other times in Chicago. We ended up getting stranded on opposite sides of the closed border for eleven months. Long story Covid related but I attended meetings in person and he virtually.
As one of the demo decisions - we opted to keep the exterior stucco on the house in hopes of saving labor and dump fees. In this scenario, extra insulation would go on top of the existing shell and shingles. The system approach was devised by our contractor and energy modeler and the folks at 475. This would later make life a little more complicated because the system was not devised by either the architects or the engineers. We thought this new approach would save money and time. Alas, It was not the game changer we’d hoped. We don’t regret having tried a new approach - a first of a kind in British Columbia. We were inspired to go over the siding by a house reno in Seattle that was featured in a 475 Building supply newsletter. we later went to visit that build in person. Think of the house as wearing a thick parka. - so thick that the roof rafters had to be extended. Many many man hours were devoted to the novel approach and time is money.
At some point someone will write a treatise on the environmental benefits of embedding old siding under new insulation. Engineer Adam Campkin of Saanich who helped on the original energy modeling (and who has remained a friend) actually suggested a study of insulating over stucco. Wall systems that essentially clip on over the existing exterior can’t be far off. Combine them will zero interest loans and real progress in reducing green house gas emissions could be made. Such a solution could legitimize and encourage wide adoption of stucco house deep reno on the island. Til then, here is what we know.
The total waste that was taken to the dump by Local Hauling our demo team is estimated at 7,000- 7,725 kg. It probably would have been nearly triple that weight if Taylor and his team had not found means to repurpose or give away material from the site. The exterior stucco weight was 4,000-4,500 kg. Waste containing lead (shingles mainly and a little painted cedar trim) was 1,500 kg. Drywall and plaster waste from inside amounted to 1,135 kg. The stucco that ended up in the dump had to go because it was on the enclosed front porch and old back lean-tos that came down altogether, or was stucco that would interfere with bay window wall prep that had to happen prior to extending the roof rafters.
Our old tub at rest waiting for a new owner.
Demolition & Deaccessioning
Many of the items we placed on Used Victoria got snapped right up - clean boards, old windows - not so with the noble tub that was no doubt original to the place and in perfectly good shape. In the end it found a good home. Strange but true. Like us, the new owner is from Chicago. She is refurbishing the tub for her house in Esquimalt. The Resources section of the site has more options to sell or buy old house parts. The more you can keep out of the dump the better. Waste not want not.
Hazardous Materials
The good news was and is - there was virtually no asbestos . The bad news is the minimum fee for removal is $1000 for two hours of work. You will want to know how big an asbestos problem you have before you buy a property and prepare to pay the minimum. For the asbestos report, head to the Planning + Design Page.
Framing
Lumber + Millwork
Once the demo was complete it came time to add back new wood (and shear walls aka plywood panels) for additional support. What is a shear wall? Dean Sharp is The House Whisperer and this 8 minute video explains why they are so crucial to the structural integrity of your house by providing ability to resist lateral motion. We made use of recycled wood from our house and neighboring renos as best we could. In the photo below, you will see repurposed wood in and between the rafters of the dormer.
We opted for quality and local whenever new was called for. Through Scott & Scott we found Canadian Bavarian Millwork & Lumber in Chemainus. CanBav is owned and operated by Georg and Eva Wörnle who came on vacation from Germany, and bought a plot of land on Salt Spring Island, then thirty years ago came to Vancouver Island to found their company. Canadian Bavarian is FSC certified, reflecting commitment to environment and community. It has taken innovative approaches to make its facilities more environmentally friendly, and its carbon footprint has been reduced significantly with the implementation of a Biomass burner and partnership with BioFlame Briquettes to recycle wood waste. Wood drying services are also available to customers harvesting logs from their own property. We used as much of their product as we could on the interior and exterior on Fernwood, except where we reused wood, or had to make emergency runs to Lumber World. Canadian Bavarian is a great operation. You can see the difference between standard lumber yard material side by side with CAN BAV product. No contest.
When COVID 19 restrictions went into effect, we were short staffed on site at the house. We went from five carpenters in February to two in March, April and May. Work was able to progress faster than would have otherwise been possible because Canadian Bavarian was able top pick up some slack. Some of the interior wood trim and flooring, and exterior shingles and boards were primed and painted, or stained and waxed on site up in Chemainus. While under ordinary circumstances it might have made sense to prep old wood, in this foreign pandemic environment it did not.
Adding Dormers
We raised the ceiling upstairs (from under 8 feet to upwards of 14 feet) and raised the dormer in the master bedroom (this required a variance permit) to afford a better view of the Olympic Mountains. For good measure the architects added a matching dormer on the north side to accommodate an upstairs bath. The house originally had only one bath. Now it has two.
Early April some of the rafter tails show.
Here we are looking out of the raised dormer
Extending the Rafter Tails
There are two downstairs bays where there is evidence of past leaks. We want to avoid a recurrence. The solution is to extend the rafter tails and the roof to provide a more substantial overhang. This entails quite a lot of work. There was a lot of salvaged material involved and a lot of manpower to undergird a more robust roof. Then there was the matter of ordering and painting soffit material. The entire south roof will be covered with solar panels to power the house.
To leave or remove the stucco in the process of creating the building envelope? That is the question. Here you see the exterior wall at the beginning of the reno.
The Game Changer that Wasn’t
When we were rebudgeting the project in the month of September, the demolition expenses ranged from $17,000 to $35,000. The low end was interior only - the higher number included stripping the old siding off the house right down to the shiplap. In the 475 Building Materials newsletter, Don and I had read about a breakthrough old house reno in Seattle in which the cladding of the house same age as ours was left on and the insulation was placed over it. En route to Chicago via Seattle in October 2019, Don paid the owners a visit and checked in with our 475 friend Shaun St Amour. We relayed the info to Taylor (our contractor), David (the architect) and Mark Bernhardt (energy modeler). We all decided to go for this approach. In the end it did not produce the savings we hoped. But, it did keep a lot of material out of the dump, and hopefully is helpful to the next guy. There are thousands of splatterdash and stucco-covered houses in town. For this city to get to net zero a simple more cost-effective solution needs to be devised.